By Paul D. Spiegel, P.E., LEED AP, President, Practical Energy Solutions 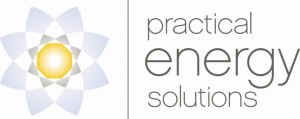
Does this sound familiar? It’s been 17 years since your rooftop HVAC units were installed, and it seems that you are spending more on repairs every month than you are on the energy costs to run the entire building for the month.
So you call in your HVAC maintenance contractor to give you a price for an “in-kind” replacement of everything that you have on the roof of your building. He/she comes back with a proposal for a one-for-one replacement, let’s say brand new packaged gas powered heating and electric cooling rooftop units, the exact same size as your older units, and higher in energy efficiency allowing you to save 5% to 6% on your energy costs.
You may be missing an opportunity to improve the energy performance of your building, increase the net asset value of your building, reduce maintenance costs for your HVAC (and your roof), and significantly extend the service life of your HVAC equipment, meaning that rather than being back at the same point in 15 years buying the next replacement, you could stretch that to 25 or 30 years.
This is a common issue in building construction, maintenance, and renovation/repair, where different options are considered and decisions are based only, or primarily, on first cost, and not the overall life cycle cost of your equipment. Life Cycle Cost Analysis (LCA) evaluates all of the costs associated with each of your options, including first cost, and the present value of future maintenance costs and energy savings, the years of service that you’ll get, and the replacement cost. Often what seems to be the more expensive option is actually the best financial choice
A case study: a client with a multi-story office building. The client had a building that was heated and cooled with 42 air source heat pumps which were nearly 20 years old, many of which were split systems that had units on the low roof area where they were exposed to the elements. Maintenance issues kept the facilities staff busy on one unit or another almost every day, and it was time to make an investment in replacement units. The rough quote from their HVAC Contractor was approximately $1.4 million. The building owner hired Practical Energy Solutions to calculate any energy savings based on the quote received, and to explore other options. Due to the improved efficiency of new units as compared to 20 year old units, they were likely to save over $100,000 per year in energy costs, or about 15% of their HVAC energy costs. If they financed 100% of the cost over 15 years, the project would break even over the 15-year loan term, at which time they would likely be shopping for new heat pumps again!
Another Option: Due to space that they had available in the basement, it was determined that a central dual temperature hydronic system could be installed in phases and be used to replace the existing heat pump system. Benefits included higher energy savings (32% instead of 15%), longer service life of the equipment, extended service life of the roof where rooftop units had been operating, reduced noise in the tenant spaces where the heat pumps were located, recovery of the heat pump closets as useable (rentable!) space, and a project that had a net positive cash flow of over $500,000 during the 15 year life of the loan. Although the initial cost was higher, nearly 100% of the project cost could be financed, and the monthly energy savings were higher than the monthly loan payments for the financing – cash flow positive from day 1, and a system that is likely to last over 25 years, and with one central chiller and one central boiler to maintain and keep parts for, and significantly reduced maintenance costs.
The moral of the story is that while an in-kind replacement can appear to be the simplest solution, you should always look at the total life cycle cost of one or two other options that can have a greater positive impact!